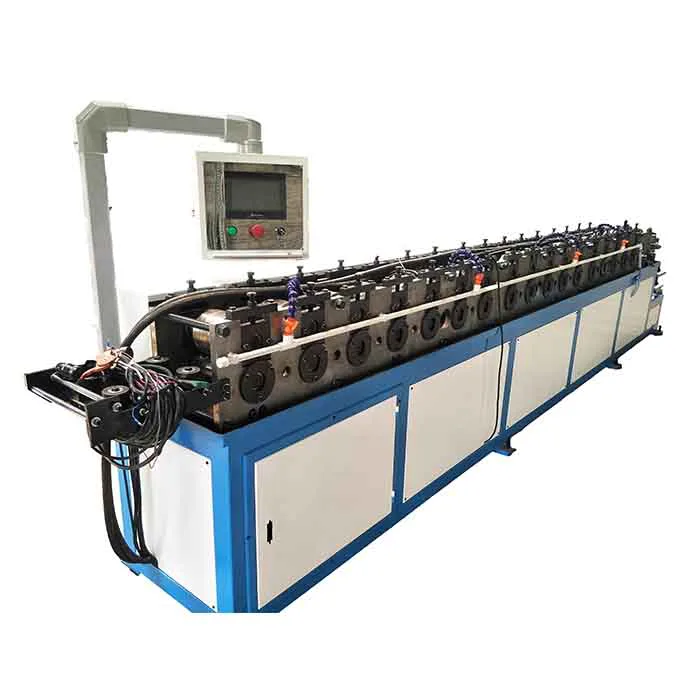
Seismic Bracing Cable Tray Roll Forming Machine
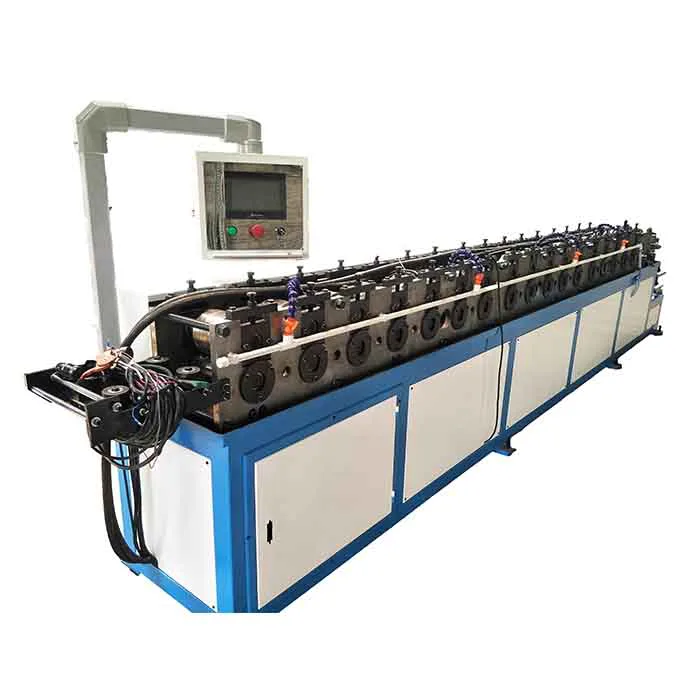
Seismic Bracing Cable Tray Roll Forming Machine
The seismic bracing cable tray and C channel roll forming machine are specially designed for customers to produce punched cold-rolled products for booms. The production process is as follows: the coils to be processed are manually placed on the unloading rack by means of a crane, then corrected, tensioned, and manually introduced into the punching die. The feeding is driven by the servo feeder, and the multi-station fixed-length feeding can be controlled by an electric system. The punched sheet material is then introduced into the forming machine, and the workpiece is formed by the steps working of the forming roller. The cut to length by the encoder. The formed workpiece passes through the cutting mold cavity. When the set length is reached, the cutting mold cuts the workpiece, and the cut workpiece is exported through the pallet, and the material is collected and transported manually.
The seismic bracing cable tray and C channel roll forming machine are specially designed for customers to produce punched cold-rolled products for booms. The production process is as follows: the coils to be processed are manually placed on the unloading rack by means of a crane, then corrected, tensioned, and manually introduced into the punching die. The feeding is driven by the servo feeder, and the multi-station fixed-length feeding can be controlled by an electric system. The punched sheet material is then introduced into the forming machine, and the workpiece is formed by the steps working of the forming roller. The cut to length by the encoder. The formed workpiece passes through the cutting mold cavity. When the set length is reached, the cutting mold cuts the workpiece, and the cut workpiece is exported through the pallet, and the material is collected and transported manually.
Single cantilever retractable uncoiler with a maximum load of 2 tons
Servo feeding and leveling device ensures feeding punching accuracy and roll forming quality
The material of the forming wheel is die steel, after heat treatment to increase the hardness
Chain or gearbox drive ensures that each forming wheel works synchronously
25-40mm side support plate is sturdy and durable
High-quality needle roller bearings ensure transmission
Hydraulic die shearing ensures that the shear port is sheared without deformation
The cylinder controls the stacking device to receive and unload the product
Whole machine occupies small area, easy to be set up and operated
Model | 41X21 | 41X41 |
Material | GI sheet, cold rolled sheet | GI sheet, cold rolled sheet |
Working thickness | 2,0-2.5 mm | 2,0-2.5 mm |
Forming extension width | 98 mm | 138 mm |
Inner diameter of material roll | φ508 mm | φ508 mm |
Roll forming station | 25 | 25 |
Roll shaft dia | φ58 mm | φ58 mm |
Side plate thickness | 30 mm | 30 mm |
Working speed | 1~5 m/min | 1~5 m/min |
Power supply for roll forming | 2*15 kw | 2*15 kw |
Power supply for hydraulic system | 7.5 kw | 7.5 kw |
Hydraulic pressure | 14 MPa | 14 MPa |