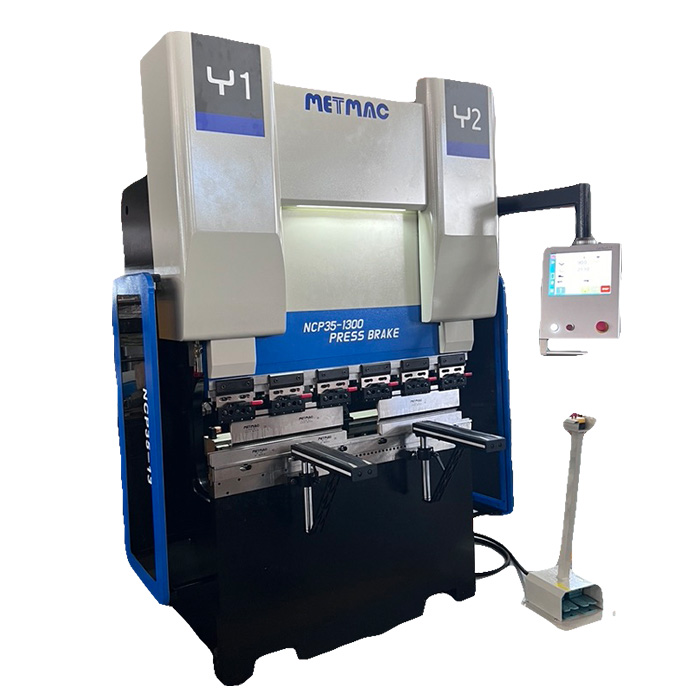
Electrical Press Brake
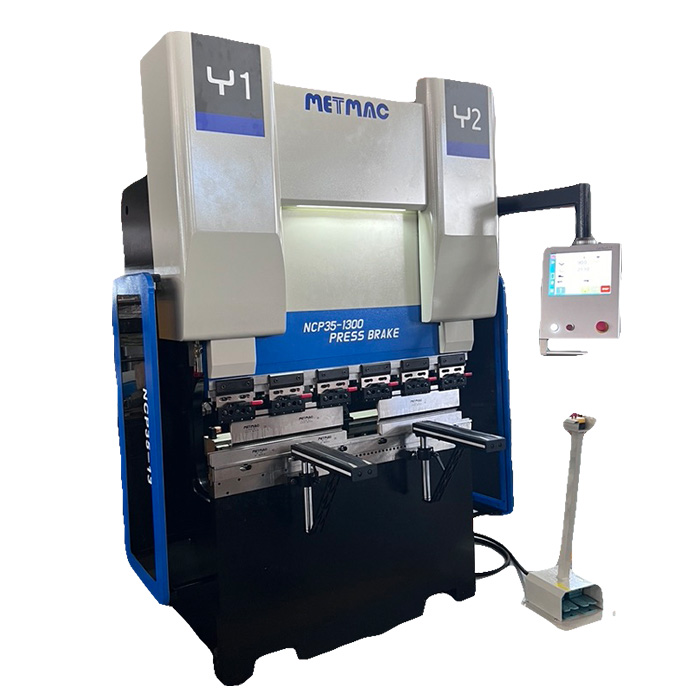
Electrical Press Brake
Electric servo press brake is mainly based on the synergy of electric servo system, CNC system, servo motor, pressure control system and workpiece clamping system.
Electric servo system: The electric servo system achieves high-precision bending by accurately controlling the motion trajectory of the slider. During the bending process, the slider slides along the bending platform driven by the oil cylinder and presses the sheet metal material. The electric servo system controls the movement of the slider according to the set parameters to ensure that the bending is carried out according to the set angle.
CNC control: The operator can input relevant parameters in the CNC system, such as the bending angle, length, material thickness, etc. The system controls the movement of the machine according to these parameters. The CNC system determines the bending angle and shape of the processed workpiece through programming to achieve high-precision control of the workpiece.
Servo motor control: The servo motor controls the bending angle and position of the workpiece by controlling the movement of the hydraulic cylinder. The high-precision control of servo motors makes it possible to bend the workpiece accurately and avoid deformation or damage.
Workpiece clamping system: In order to ensure that the workpiece in the bending process will not be shifted or misaligned, servo CNC bending machine is usually equipped with a workpiece clamping system, firmly clamped workpiece, to ensure that it is in the bending process to maintain a stable position and attitude.
In summary, the electric servo press brake, through the precise control of the electric servo system, the programming of the CNC system, the precise drive of the servo motor, the appropriate adjustment of the pressure control system and the workpiece clamping system firmly clamped, together to achieve the accurate bending processing of sheet metal, with high precision, high efficiency, energy saving and other advantages.
Electric servo press brake is mainly based on the synergy of electric servo system, CNC system, servo motor, pressure control system and workpiece clamping system.
Electric servo system: The electric servo system achieves high-precision bending by accurately controlling the motion trajectory of the slider. During the bending process, the slider slides along the bending platform driven by the oil cylinder and presses the sheet metal material. The electric servo system controls the movement of the slider according to the set parameters to ensure that the bending is carried out according to the set angle.
CNC control: The operator can input relevant parameters in the CNC system, such as the bending angle, length, material thickness, etc. The system controls the movement of the machine according to these parameters. The CNC system determines the bending angle and shape of the processed workpiece through programming to achieve high-precision control of the workpiece.
Servo motor control: The servo motor controls the bending angle and position of the workpiece by controlling the movement of the hydraulic cylinder. The high-precision control of servo motors makes it possible to bend the workpiece accurately and avoid deformation or damage.
Workpiece clamping system: In order to ensure that the workpiece in the bending process will not be shifted or misaligned, servo CNC bending machine is usually equipped with a workpiece clamping system, firmly clamped workpiece, to ensure that it is in the bending process to maintain a stable position and attitude.
In summary, the electric servo press brake, through the precise control of the electric servo system, the programming of the CNC system, the precise drive of the servo motor, the appropriate adjustment of the pressure control system and the workpiece clamping system firmly clamped, together to achieve the accurate bending processing of sheet metal, with high precision, high efficiency, energy saving and other advantages.
1. High Precision & Accuracy
– Utilizes advanced CNC control systems for precise bending angles and repeatability.
– Servo-electric drive ensures consistent performance with minimal deviation.
2. Energy Efficiency
– Fully electric operation reduces energy consumption compared to hydraulic systems.
– No hydraulic oil required, lowering operational costs and environmental impact.
3. Fast & Quiet Operation
– Electric motors provide rapid response and high-speed bending without noise pollution.
– Smooth motion control improves productivity.
4. User-Friendly CNC Interface
– Intuitive touchscreen controls with programmable memory for multiple bending sequences.
– Supports offline programming and simulation for efficient workflow.
5. Low Maintenance
– Fewer mechanical parts and no hydraulic components reduce wear and maintenance needs.
– Long-lasting performance with minimal downtime.
6. Space-Saving Design
– Compact structure ideal for workshops with limited space.
7. Safety Features
– Equipped with light curtains, emergency stops, and overload protection for operator safety.
8. Versatile Applications
– Suitable for bending various materials (steel, aluminum, stainless steel) in industries like automotive, aerospace, and metal fabrication.
Description | Unit | Parameter |
Bending pressure | Ton | 35 |
Working table length | mm | 1300 |
Workbench width | mm | 60 |
Column spacing | mm | 1000 |
Stock (Y-axis) | mm | 170 |
Maximum opening height | mm | 400 |
Throat depth | mm | 300 |
Slider speed (no-load) | mm/s | 230 |
Slide speed (work) | mm/s | 12 |
Slider Speed (Return) | mm/s | 230 |
Maximum rear trip (X axis) | mm | 500 |
Power of motor | kw | 15 |
Dimensions | mm | 1800*1340*2300 |
Weight | kg | 3000 |